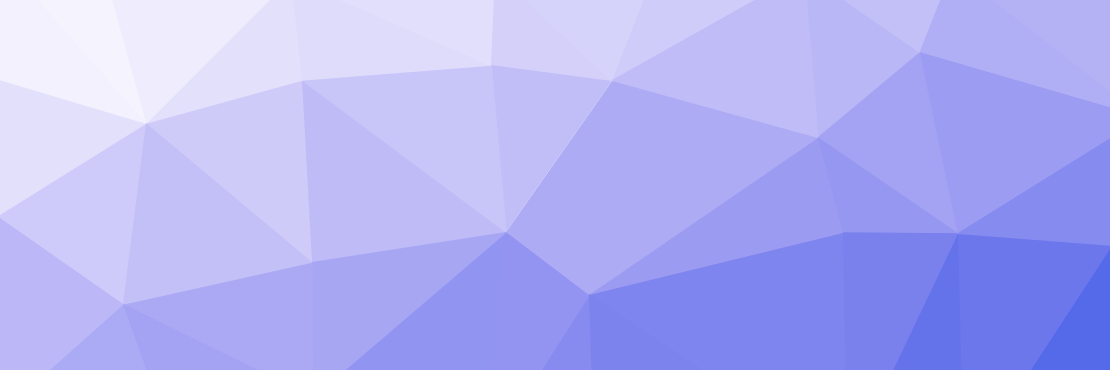


CESAR ORUGA
PremiumIndustrial Engineer, ARAYMOND JAPAN
Kanagawa, Japan
followers
7
following
0
1. Responsible for the improvement of assembly machine, assembly process and all technical activities, establish of new production lines, introduction of new equipment, planning and execution of new projects (quality, cost, delivery time, safety).
2. Understanding customer requests and negotiating with key person in other departments (managers, project managers, etc.) to realize those requests.
3. Promote information sharing, documentation, and standardization regarding know-how in field of responsibility.
See detailed Responsibilities in my Resume.
2. Understanding customer requests and negotiating with key person in other departments (managers, project managers, etc.) to realize those requests.
3. Promote information sharing, documentation, and standardization regarding know-how in field of responsibility.
See detailed Responsibilities in my Resume.
Skills: 5s continuous improvement kaizen lean manufacturing manufacturing root cause analysis value stream mapping
Industrial Engineer
January 2024 - present (1 year 7 months)
Mission
1. Responsible for the improvement of Assembly machine, assembly process and all technical activities, establish of new production lines, introduction of new equipment, planning and execution of new projects (quality, cost, delivery time, safety).
2. Understanding customer requests and negotiating with key person in other departments (managers, project managers, etc.) to realize those requests.
3. Promote information sharing, documentation, and standardization regarding know-how in field of responsibility.
Responsibilities
• Process design:
Design a highly productive manufacturing process Design a highly efficient manufacturing process by considering the selection of manufacturing method (automatic, semi-automatic, manual line), optimization of process flow, layout of production equipment, etc.
• Production equipment development:
Based on the process design described above, select equipment manufacturers, and develop automatic and semi-automatic machines, as well as develop and manage jigs for manual lines. Design and develop high accuracy assembly process equipment using automation technology, robot technology, or simple jigs.
• Mass production start-up:
Process development from prototype to mass production and improve productivity to ensure a smooth transition to mass production. Responsible for launching mass production, Train the operators, and managing productivity for mass production.
• Evaluate the entire existing production process and propose and implement measures to increase productivity and improve quality.
• Plan and execute maintenance activities to keep existing production lines and equipment in good working condition. Also responsible for troubleshooting and preventive maintenance activities.
• Develop the equipment and prepare for mass production of new products using existing facilities (feasibility checks, prototyping and arranging new jigs, etc.).
• Technical Support: Consider and provide specific technical solutions to technical problems and issues at manufacturing sites. Assist troubleshooting and maintenance of production lines to support the smooth running of production activities.
• IATF16949, ISO14001, CAPEX/OPEX related tasks and Safety-related activities
• Other tasks instructed, requested, or assigned by superiors and team members
• Manage safety in the workplace and at each process line, promote safety first initiatives, and aim for zero accidents.
• As Industrial Engineer, responsible for providing active support to the Assembly Manager, Quality Leader, Shift Leader, and Operators regarding technical tasks.
• Plan and establish new production lines, introduction of new equipment, and improvement of existing process lines to achieve the required product quality, manufacturing costs, and stable supply.
• Proactively support relevant personnel in improving rejects, quality control, downtime, and output during production, which are directly related to manufacturing costs.
• Improve the unique technology and core competencies of Raymond Japan's assembly process and work to make them company assets.
• Work with team members (Injection Molding, Quality Control, Operation System) to improve production efficiency, quality assurance and process design.
1. Responsible for the improvement of Assembly machine, assembly process and all technical activities, establish of new production lines, introduction of new equipment, planning and execution of new projects (quality, cost, delivery time, safety).
2. Understanding customer requests and negotiating with key person in other departments (managers, project managers, etc.) to realize those requests.
3. Promote information sharing, documentation, and standardization regarding know-how in field of responsibility.
Responsibilities
• Process design:
Design a highly productive manufacturing process Design a highly efficient manufacturing process by considering the selection of manufacturing method (automatic, semi-automatic, manual line), optimization of process flow, layout of production equipment, etc.
• Production equipment development:
Based on the process design described above, select equipment manufacturers, and develop automatic and semi-automatic machines, as well as develop and manage jigs for manual lines. Design and develop high accuracy assembly process equipment using automation technology, robot technology, or simple jigs.
• Mass production start-up:
Process development from prototype to mass production and improve productivity to ensure a smooth transition to mass production. Responsible for launching mass production, Train the operators, and managing productivity for mass production.
• Evaluate the entire existing production process and propose and implement measures to increase productivity and improve quality.
• Plan and execute maintenance activities to keep existing production lines and equipment in good working condition. Also responsible for troubleshooting and preventive maintenance activities.
• Develop the equipment and prepare for mass production of new products using existing facilities (feasibility checks, prototyping and arranging new jigs, etc.).
• Technical Support: Consider and provide specific technical solutions to technical problems and issues at manufacturing sites. Assist troubleshooting and maintenance of production lines to support the smooth running of production activities.
• IATF16949, ISO14001, CAPEX/OPEX related tasks and Safety-related activities
• Other tasks instructed, requested, or assigned by superiors and team members
• Manage safety in the workplace and at each process line, promote safety first initiatives, and aim for zero accidents.
• As Industrial Engineer, responsible for providing active support to the Assembly Manager, Quality Leader, Shift Leader, and Operators regarding technical tasks.
• Plan and establish new production lines, introduction of new equipment, and improvement of existing process lines to achieve the required product quality, manufacturing costs, and stable supply.
• Proactively support relevant personnel in improving rejects, quality control, downtime, and output during production, which are directly related to manufacturing costs.
• Improve the unique technology and core competencies of Raymond Japan's assembly process and work to make them company assets.
• Work with team members (Injection Molding, Quality Control, Operation System) to improve production efficiency, quality assurance and process design.
Maintenance Engineer/Leader
March 2021 - December 2023 (2 years 10 months)
Mission
Responsible for the Maintenance and repair of Production Equipment related to Injection molding process and Plant Equipment.
Role involves contributing to Manufacturing cost, Product Quality & Manufacturing
lead time. It is roughly divided into four fields:
1. post-maintenance to deal with equipment troubles
2. Preventive maintenance to prevent equipment troubles in advance
3. Predictive maintenance to identify and maintain signs of failure
4. and Safety Management related to Equipment.
Scope of responsibility: Molding process equipment related such as Molding Machine,
Product taking-out attachment, Temperature controller, Dryer, AGF, Automatic mold warehouse, Hoist Crane, Chiller, etc.).
Compressor, Hot runner parts and factory equipment such as electricity, firefighting, and air conditioning equipment.
Post-maintenance: Respond to equipment failure, production capacity & defective products.
Preventive maintenance: Perform maintenance work on a regular basis.
Internal and External according to the maintenance plan.
Predictive maintenance: Acquire data related to equipment, identify signs of failure, and perform maintenance.
Safety Management: To ensure work safety for staff, operators, and external contractors.
Other related work (proposal of new equipment, improvement activities, 5S activities, support for operation teams, Participation in global meetings, etc.)
Responsibilities
< Post-Maintenance related activities>
To coordinate with staff and external contractors to perform immediate Action for
Equipment failure, production capacity decrease, defective product occurrence:
Incorporate failure details into preventive and predictive maintenance and strive to minimize failures and downtime.
To ensure eliminate air leakage to all injection molding process related equipment.
< Preventive Maintenance related activities>
To lead creation and manage maintenance plan for all injection molding process related equipment.
To Organize and Manage Equipment daily inspections.
To Organize and manage equipment spare parts management system.
< Predictive Maintenance related activities >
To perform and/or collect, capabilities of equipment and process.
To manage equipment maintenance plan.
< Safety management related activities >
Take immediate action and measures for potential unsafe work condition. If the safety assessment is not sufficient, consult with the team or superior, or perform patrol take measures to identified unsafe condition areas.
Responsible for safety management, when requesting maintenance from outside company.
< Other activities >
Proactively introduce proposals, considering more efficient for equipment, systems, tools and work methods.
Perform improvement activities, own duties and teamwork related.
Perform 5S activities such as equipment, tools, and shelves related to the site.
Provide advice and work support for problems of the operations team.
Become a member of the global maintenance community and contribute to the network and Raymond Japan.
Operations that the superior and the general manager of the department deem necessary.
Nature and Scope of Work
Strive to minimize downtime due to equipment failure by combining various types of maintenance.
Thorough safety management for each facility, manage to eliminate occupational accidents caused by equipment.
Always be aware of maintenance costs such as budgeting for maintenance and spare parts and managing performance.
Although the reporting line is different, we work in cooperation with the molding manager as a member of the molding team,
In addition, based on the knowledge and experience, actively provide operational support, training, and exchange of opinions.
Workplace work environment, manufacturing costs, Environmental aspect, proactively consider and propose more efficient equipment and work methods.
Be careful not to leak the information you have obtained or created, Various statistics, when creating management documentations, make sure that there are no mistakes on the deadline date.
Responsible for the Maintenance and repair of Production Equipment related to Injection molding process and Plant Equipment.
Role involves contributing to Manufacturing cost, Product Quality & Manufacturing
lead time. It is roughly divided into four fields:
1. post-maintenance to deal with equipment troubles
2. Preventive maintenance to prevent equipment troubles in advance
3. Predictive maintenance to identify and maintain signs of failure
4. and Safety Management related to Equipment.
Scope of responsibility: Molding process equipment related such as Molding Machine,
Product taking-out attachment, Temperature controller, Dryer, AGF, Automatic mold warehouse, Hoist Crane, Chiller, etc.).
Compressor, Hot runner parts and factory equipment such as electricity, firefighting, and air conditioning equipment.
Post-maintenance: Respond to equipment failure, production capacity & defective products.
Preventive maintenance: Perform maintenance work on a regular basis.
Internal and External according to the maintenance plan.
Predictive maintenance: Acquire data related to equipment, identify signs of failure, and perform maintenance.
Safety Management: To ensure work safety for staff, operators, and external contractors.
Other related work (proposal of new equipment, improvement activities, 5S activities, support for operation teams, Participation in global meetings, etc.)
Responsibilities
< Post-Maintenance related activities>
To coordinate with staff and external contractors to perform immediate Action for
Equipment failure, production capacity decrease, defective product occurrence:
Incorporate failure details into preventive and predictive maintenance and strive to minimize failures and downtime.
To ensure eliminate air leakage to all injection molding process related equipment.
< Preventive Maintenance related activities>
To lead creation and manage maintenance plan for all injection molding process related equipment.
To Organize and Manage Equipment daily inspections.
To Organize and manage equipment spare parts management system.
< Predictive Maintenance related activities >
To perform and/or collect, capabilities of equipment and process.
To manage equipment maintenance plan.
< Safety management related activities >
Take immediate action and measures for potential unsafe work condition. If the safety assessment is not sufficient, consult with the team or superior, or perform patrol take measures to identified unsafe condition areas.
Responsible for safety management, when requesting maintenance from outside company.
< Other activities >
Proactively introduce proposals, considering more efficient for equipment, systems, tools and work methods.
Perform improvement activities, own duties and teamwork related.
Perform 5S activities such as equipment, tools, and shelves related to the site.
Provide advice and work support for problems of the operations team.
Become a member of the global maintenance community and contribute to the network and Raymond Japan.
Operations that the superior and the general manager of the department deem necessary.
Nature and Scope of Work
Strive to minimize downtime due to equipment failure by combining various types of maintenance.
Thorough safety management for each facility, manage to eliminate occupational accidents caused by equipment.
Always be aware of maintenance costs such as budgeting for maintenance and spare parts and managing performance.
Although the reporting line is different, we work in cooperation with the molding manager as a member of the molding team,
In addition, based on the knowledge and experience, actively provide operational support, training, and exchange of opinions.
Workplace work environment, manufacturing costs, Environmental aspect, proactively consider and propose more efficient equipment and work methods.
Be careful not to leak the information you have obtained or created, Various statistics, when creating management documentations, make sure that there are no mistakes on the deadline date.
Project/Process Engineer
August 2015 - March 2021 (5 years 8 months)
Mission
● To lead all Industrialization activities for Damper line and MPO Pendulum Project PTM
SQCD (Safety, Quality, Cost, Delivery)
● To lead the Industrialization of the new Project/Product for P1 and P0.
● Capitalize and share the know-how of Industrial Processes & Manufacturing.
● To lead Design/Introduction of New Equipment and New Production lines.
Responsibilities
● Industrialization
○ To Manage layout and equipment introduction using IPROM as indicator.
○ Responsible for equipment and production lines development
○ Generate equipment specification, design of tools and fixture
○ Responsible to lead creation of PFMEA and Control Plan
○ To lead validation of supplier proposal and negotiation to meet the requirement.
○ To define the acceptance criteria of new equipment subject for acceptance
○ To perform pre acceptance and acceptance of the equipment at supplier site
○ To perform trials on the lines and deliver reports
○ To build action plans and follow up to be ready for FDPR
○ To perform and/or collect, process and equipment capabilities.
○ To create and execute production related document
(Inspection standards, operation sheet)
○ To create a future plan for layout and equipment based on MTP
● Mass production
○ To monitor SQCDM and propose improvement to all existing production lines
○ To monitor the performance of equipment, and always in mind, optimization
○ To work on Cycle time reduction to optimize investments, material & labor costs
○ To support APU activities (training, analysis, problem solving)
○ To be in contact with suppliers of equipment, tool (improvement, support)
● Standardization
○ To create local standards through P1, P0 and equipment industrialization
○ To promote RAISE standards from local standards which should be shared among PG
○ To create, apply and maintain local work procedure
● Health Safety & Environment
○ To respect and reflect local regulation for safety and environment to equipment design
○ To respect of Health Safety and Environment procedures of Valeo Group
○ Maintain the 5S and report issues
● Miscellaneous
○ To respect ISO 9001, IATF 16949, ISO 14001 and OHSAS
● To lead all Industrialization activities for Damper line and MPO Pendulum Project PTM
SQCD (Safety, Quality, Cost, Delivery)
● To lead the Industrialization of the new Project/Product for P1 and P0.
● Capitalize and share the know-how of Industrial Processes & Manufacturing.
● To lead Design/Introduction of New Equipment and New Production lines.
Responsibilities
● Industrialization
○ To Manage layout and equipment introduction using IPROM as indicator.
○ Responsible for equipment and production lines development
○ Generate equipment specification, design of tools and fixture
○ Responsible to lead creation of PFMEA and Control Plan
○ To lead validation of supplier proposal and negotiation to meet the requirement.
○ To define the acceptance criteria of new equipment subject for acceptance
○ To perform pre acceptance and acceptance of the equipment at supplier site
○ To perform trials on the lines and deliver reports
○ To build action plans and follow up to be ready for FDPR
○ To perform and/or collect, process and equipment capabilities.
○ To create and execute production related document
(Inspection standards, operation sheet)
○ To create a future plan for layout and equipment based on MTP
● Mass production
○ To monitor SQCDM and propose improvement to all existing production lines
○ To monitor the performance of equipment, and always in mind, optimization
○ To work on Cycle time reduction to optimize investments, material & labor costs
○ To support APU activities (training, analysis, problem solving)
○ To be in contact with suppliers of equipment, tool (improvement, support)
● Standardization
○ To create local standards through P1, P0 and equipment industrialization
○ To promote RAISE standards from local standards which should be shared among PG
○ To create, apply and maintain local work procedure
● Health Safety & Environment
○ To respect and reflect local regulation for safety and environment to equipment design
○ To respect of Health Safety and Environment procedures of Valeo Group
○ Maintain the 5S and report issues
● Miscellaneous
○ To respect ISO 9001, IATF 16949, ISO 14001 and OHSAS

Don Bosco Technical Institute
Associate’s degree
Mechanical Engineering Technology
1993 - 1994
Similar members
Engineer, EAZI General Trading
Software Engineer
CAD Mechanical Design Engineer well versed in UNIGRAPHICS NX software 3D Modeler, MAHLE
Goodyear Tire and Rubber Company - Senior Automotive Expert / Tokyo, Japan
Engineer, ZF Japan
Engineer, Ltd.